24-Mar-2025
Single beam bridge crane and electric hoist installation construction plan
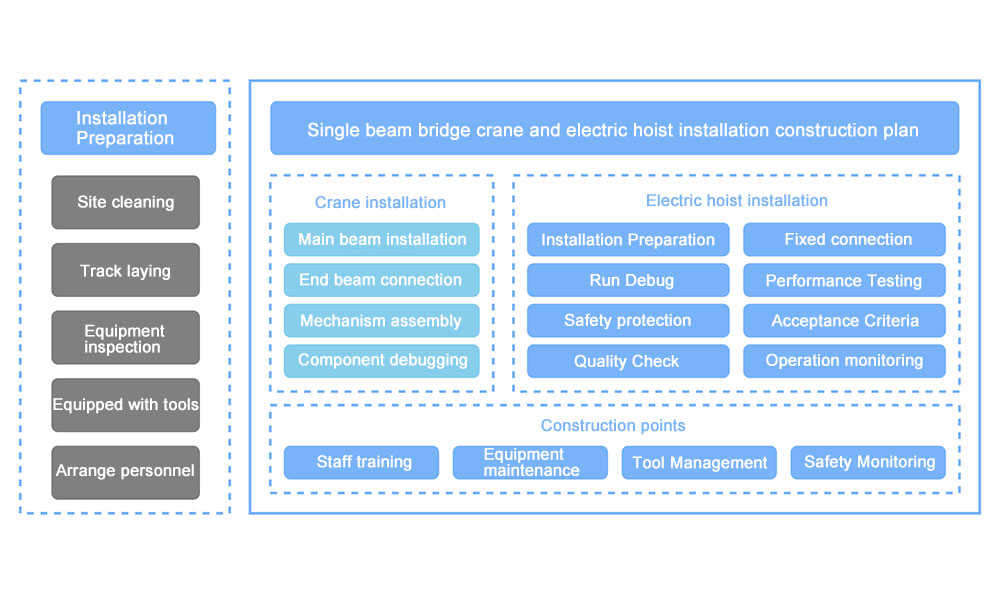
As an indispensable lifting equipment in modern industry, the rationality and accuracy of the installation and construction plan of single-beam bridge cranes and electric hoists are directly related to the subsequent operation efficiency and safety of the equipment. This plan aims to elaborate the whole process from equipment and material preparation to installation site layout, to specific installation steps and commissioning, and finally to the final safety inspection and acceptance. Through careful planning and strict operation, ensure that single-beam bridge cranes and electric hoists can stably and efficiently serve various industrial production scenarios. This article will deeply explore the key points and precautions of each installation link, aiming to provide relevant personnel with a comprehensive and practical installation and construction guide.
Overview of Installation and Construction Plan
As important lifting equipment in modern industrial plants, the formulation and implementation of the installation and construction plan of single-beam bridge cranes and electric hoists are directly related to the stable operation and operation safety of the equipment. This plan aims to elaborate the installation process, technical requirements and safety measures of single-beam bridge cranes and electric hoists in detail to ensure that the installation process is standardized, efficient and safe. Through the systematic planning of pre-installation preparation, site layout, installation steps, commissioning and acceptance, the high-quality completion of equipment installation is achieved. At the same time, this plan also emphasizes quality control and safety protection measures during the installation process to ensure the safety and smooth progress of the entire installation process.
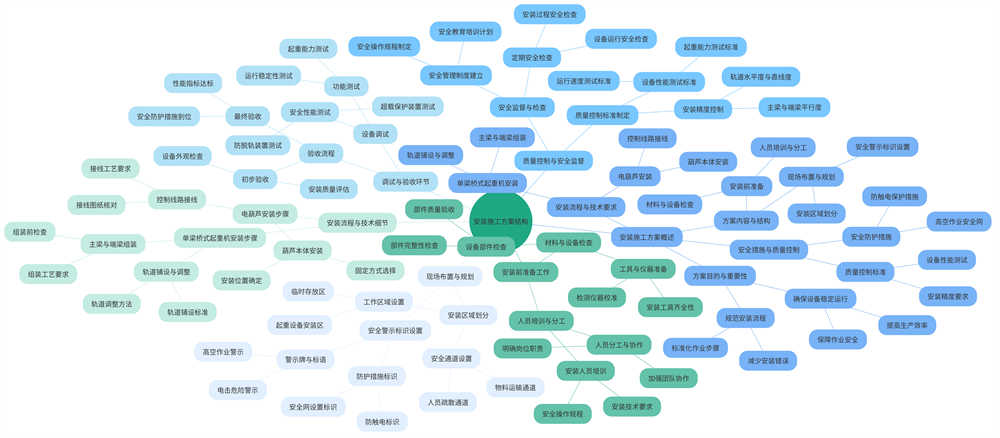
Equipment and material preparation
Single-beam bridge crane component inspection
Before formal installation, all components of the single-beam bridge crane need to be carefully and comprehensively inspected. This includes but is not limited to key components such as the main beam, end beam, lifting mechanism, operating mechanism, and electrical system. For the main beam and end beam, the inspection content mainly covers the integrity of the components, whether there are cracks, deformations and other appearance damage, as well as dimensional accuracy and matching clearance. For the lifting mechanism and operating mechanism, it is necessary to check the fastening of each component, such as whether the bolts, nuts, etc. are loose or fall off, the wear of each component, such as whether the gears, bearings, etc. are severely worn, and the lubrication of each component, such as whether the lubricating oil is sufficient and the lubrication is good. For the electrical system, it is necessary to check whether the electrical components are intact, whether the wiring is firm and reliable, and whether the insulation resistance meets the requirements. Ensure that all components meet the design requirements and are free of defects or damage.
Preparation of electric hoists and related accessories
As an important supporting equipment for cranes, the preparation work before assembly of electric hoists is also crucial. It is necessary to count and inspect the accessories such as the electric hoist body, wire rope, hook, controller, etc. Check whether the structure of the electric hoist body is complete, whether there is any deformation or damage, and whether the fastening of each component is good, especially the loose parts such as bolts and nuts. The wear of the wire rope is also the focus of the inspection, such as whether there are problems such as broken wires and deformation, as well as the wear of the hook, to ensure that it meets the safety standards. For key electrical components such as controllers, it is necessary to check whether their performance is stable and reliable, and whether the wiring is intact. At the same time, prepare the necessary connectors, fasteners and safety protection devices according to the installation requirements. These connectors and fasteners include bolts, nuts, washers, etc. of various specifications, and safety protection devices such as overload protectors and limiters.
Installation tools and equipment preparation
To ensure the smooth progress of the installation process, the required installation tools and equipment need to be prepared in advance. This includes but is not limited to lifting machinery, welding equipment, power tools, measuring instruments, etc. When preparing lifting machinery, ensure that its performance is stable and reliable, and the operator has the corresponding qualifications and experience. Welding equipment needs to check whether its power connection is stable and reliable, and whether accessories such as welding guns and welding clamps are intact. Power tools such as drilling machines and grinders also need to be inspected and maintained. Measuring instruments such as levels and steel rulers also need to be inspected and maintained to ensure their accuracy and reliability. All tools and equipment must be calibrated and tested to ensure stable, safe and reliable performance.
Installation site preparation and layout
Installation site cleaning and planning
Before installation, the installation site must be thoroughly cleaned to remove all debris and obstacles that are not related to the installation, including but not limited to ground debris, hanging objects, wires and cables, and other materials that may affect the installation process or cause safety hazards. The space in the site should be reasonably planned, and key areas such as the equipment foundation position, hoisting channel, and personnel operation space should be determined according to the size, weight and installation requirements of the equipment. Clearly set up transportation channels to ensure that equipment and hoisting tools can enter and exit smoothly; establish a stable working platform to meet the installation personnel’s standing and operating needs during the operation; set up eye-catching safety warning signs at key locations, such as “No fireworks” and “dangerous areas”, to remind on-site personnel to pay attention to safety and avoid potential risks.
Determination of the installation position of the lifting equipment
During the installation process, the actual structural bearing capacity of the plant, the size parameters of the equipment itself, and the specific operation requirements must be combined, and the best installation position of the crane must be determined through precise calculation and measurement. This step involves the overall consideration of many factors such as the equipment lifting path, the connection method between equipment, and the power supply to ensure that the crane can provide sufficient lifting height and coverage when working. During the installation process, it is also necessary to strictly follow the design drawings and standard specifications, accurately install the main beam, end beam and running track of the crane, and through precise measurement and marking methods, ensure that all parameters meet the design requirements and ensure the stability and safety of the crane in subsequent use.
Safety protection measures are set up
In order to ensure the life safety of on-site staff and the integrity of equipment, perfect safety protection measures must be set up at the installation site. This includes but is not limited to setting up a safety net, that is, setting up a strong safety net around the site to prevent injuries caused by accidental falling objects; setting up guardrails, that is, setting up a stable guardrail around the dangerous area where people may approach to prevent unrelated people from approaching; installing warning lights and alarms and other equipment to remind on-site personnel to pay attention to safety and avoid accidents such as collisions or squeezing. At the same time, according to the actual situation on site, detailed safety operating procedures and emergency plans are formulated to clarify the safety precautions during the installation process and the measures to deal with emergencies to ensure the safety of personnel and equipment throughout the installation process.
Single beam bridge crane installation steps
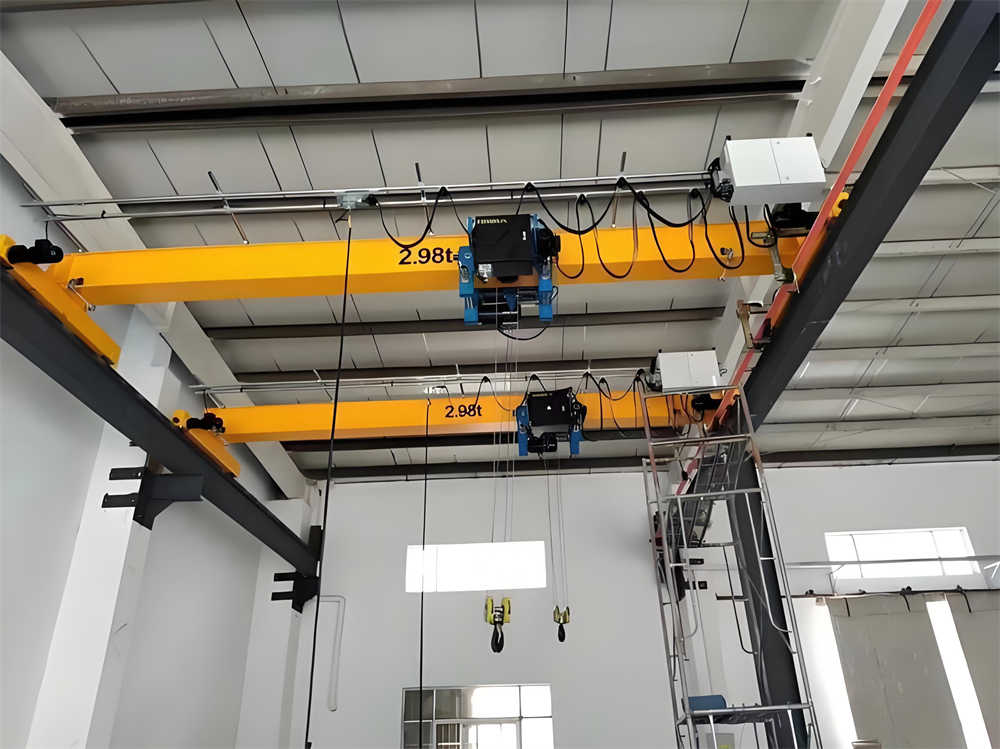
Main beam and end beam assembly
According to the design drawings and technical requirements, the main beam and end beam are assembled accurately. First, the main beam and end beam are carefully inspected to confirm that their size, shape and material meet the design requirements. Then, according to the instructions of the drawings, the main beam and end beam are pre-assembled, and high-strength bolts or welding are used to ensure the stable connection between the main beam and the end beam. During the connection process, attention should be paid to maintaining the horizontality and verticality to ensure the stability and safety of the crane.
Lifting mechanism installation
The lifting mechanism is installed on the main beam to ensure the correct installation and coordination of the drum, wire rope, hook and other components. During the installation process, it is necessary to check whether the drum rotates flexibly, whether the wire rope is firmly fixed, and whether the lifting and lowering of the hook is stable. At the same time, the electrical control system of the lifting mechanism is debugged to ensure its smooth and accurate operation. During the debugging process, the sensitivity and reliability of the control system should be checked to ensure the safety and stability of the crane.
Operating mechanism installation
Install the operating mechanism, including the drive device, wheel set and track. During the installation process, ensure the horizontality and verticality of the wheel group to ensure the smooth operation of the crane on the track. At the same time, check whether the installation position of the drive device is correct and whether the transmission mechanism is flexible and reliable. After the installation is completed, the operating mechanism should be debugged and tested to ensure its smooth and accurate operation.
Electrical system installation and debugging
Install the electrical system of the crane according to the electrical design drawings and specifications. Including the installation and wiring of components such as control cabinets, cables, motors, sensors, etc. During the installation process, ensure the correctness and reliability of the wiring to avoid electrical failures. Then, debug and test the electrical system, including testing of control systems, protection devices, display devices, etc. During the debugging process, check whether the system control is accurate, whether the operation is reliable, and whether the display is clear.
Electric hoist installation and debugging
Electric hoist assembly and inspection
Before formal installation, assemble and inspect the electric hoist. Ensure that all components such as lifting mechanism, motor, reducer, drum, pulley group, walking wheel group, electrical control system, etc. are installed correctly, and fasteners such as bolts, nuts, pins, etc. are firm and not loose. For electrical connections, ensure that all terminals, cables and other components are connected reliably without any false connection or short circuit. At the same time, conduct a no-load test run on the electric hoist, run it under no-load conditions, and check its running stability, braking performance and the effectiveness of safety protection devices. Observe the stability of the electric hoist during start-up, operation and stop, confirm the braking effect of its braking system under various working conditions, and whether the safety protection devices such as overload protection and limit protection can work accurately and effectively.
Hoisting and positioning of electric hoist
Use appropriate lifting machinery to hoist the electric hoist to the predetermined position. During the hoisting process, pay attention to maintaining the balance of the electric hoist to avoid damage caused by swinging or tilting. Ensure that the connection between the electric hoist and the main beam of the crane is stable and the position is accurate through precise adjustment. During the installation process, use special tools for precise adjustment to ensure that the installation position of the electric hoist is fully matched with the main beam of the crane, and ensure that all connecting parts such as bolts and nuts are firmly fastened without any looseness.
Electric hoist operation and debugging
Perform a load test run on the electric hoist to check its operating performance under different working conditions. Including the testing and adjustment of parameters such as lifting speed, running speed, and braking distance. During the load trial operation, the various performance parameters of the electric hoist are accurately tested and adjusted. The lifting speed test is intended to confirm whether the speed of the electric hoist when lifting heavy objects meets the design requirements; the running speed test involves checking the speed stability of the electric hoist when running on the track; the braking distance test is to verify the effectiveness and safety of the electric hoist during braking. At the same time, the safety protection device of the electric hoist is functionally verified to ensure its sensitivity and reliability. During the load trial operation, the various safety protection devices of the electric hoist also need to be functionally verified. These devices include but are not limited to overload protection, limit protection, etc. By simulating various extreme situations in actual working conditions, it is verified whether these devices can respond correctly at the first time to ensure the safe and stable operation of the entire system.
Safety inspection and acceptance
Installation quality inspection
After the installation of the crane is completed, a comprehensive and detailed installation quality inspection must be carried out. This link covers many aspects. First, focus on the connection parts of the main beam and the end beam to confirm whether the welding quality, bolt tightening degree and other forms of connection meet the design strength requirements. At the same time, professional measurement methods are used to check whether the horizontality and verticality of the main beam and the end beam after installation are within the allowable error range to ensure that the overall structure is stable and the geometric dimensions are accurate. Secondly, dynamic tests are carried out on the functions of the lifting mechanism and the operating mechanism to observe their smoothness, stability and responsiveness under load during operation, and to confirm that the wear of various mechanical transmission parts such as gears and chains is within a reasonable range and there is no abnormal noise or vibration. For the electrical system, carefully check whether the connections of all components such as terminals, switch cabinets and controllers are firm and reliable, whether the logic control is accurate, and whether the display of various indicator lights is normal, and try to perform linkage debugging under simulated working conditions to verify the functional integrity and safety of the electrical system.
Safety performance testing
In the application process of the crane, it is very important to regularly test its safety performance. These tests cover multiple key points. The first task is to evaluate the load-bearing capacity of the crane, and to determine whether it meets the design load-bearing requirements through professional mechanical tests to avoid structural damage due to overload or long-term fatigue load. Secondly, stability testing is also an important part that cannot be ignored. It is necessary to simulate actual working conditions to evaluate the overturning risk of the crane under different working conditions to ensure that it can maintain sufficient stability under various working conditions. The detection of braking performance is also important. The braking distance, braking deceleration and other parameters of each operating mechanism and lifting mechanism under no-load and load conditions are tested to ensure that the operation can be stopped quickly and effectively in an emergency to avoid safety accidents. In addition, the effectiveness verification of safety protection devices is also an indispensable part, including but not limited to limit switches, emergency stop buttons, guardrails, track sweeping plates and other safety protection facilities to ensure that they can play their due protective role at critical moments.
Acceptance standards and processes
In order to ensure that the installation quality and safety performance of the crane meet the design intent and industry specifications, rigorous and detailed acceptance standards and processes must be formulated. First, an acceptance team including but not limited to the installation unit, user unit, supervision unit and relevant industry experts is organized to participate in the acceptance work. During the acceptance process, the installation quality of the crane is comprehensively checked by various methods such as on-site inspection, performance testing and data review. On-site inspection includes inspection of the appearance of the whole machine to confirm whether the installation position of each component is accurate; performance testing covers the inspection of various functional characteristics of the crane, such as whether the lifting weight, running speed, accuracy, etc. meet the design requirements; data review includes review of relevant documents such as record files, product certificates, test reports, etc. during the installation process.
Installation and construction precautions
Personnel safety and protection measures
During the installation and construction process, a series of detailed safety operating procedures and protection measures must be strictly followed to ensure the personal safety and health of the operators. First of all, each operator should be equipped with and correctly use personal protective equipment including but not limited to safety helmets, safety belts, protective glasses, protective masks, etc. to ensure that they are always under control during the construction process to avoid injuries caused by accidental slips, falling objects, splashes, etc. Secondly, the construction unit should establish a complete on-site safety management system, set up full-time safety officers for on-site supervision, and regularly carry out safety education and training activities to improve the safety awareness and operating skills of all operators. At the same time, conspicuous safety warning signs and isolation facilities should be set up in the construction area to prevent unrelated personnel from entering the operation area and ensure that the operators have a clear understanding of the on-site environment.
Equipment protection and maintenance
During the equipment installation and commissioning phase, it is important to pay attention to the proper protection and daily maintenance of the equipment. For each device, necessary anti-vibration and anti-collision measures should be taken, such as using special packaging materials, foam pads, etc. to reduce the risk of mechanical damage during transportation and hoisting; for precision parts or vulnerable parts, a detailed inspection should be carried out before and after installation to ensure that there are no scratches or impact marks to avoid equipment performance degradation or even scrapping due to small losses. In addition, according to the characteristics of the equipment and operating requirements, the equipment maintenance plan should be regularly implemented, including but not limited to cleaning and dust removal, lubrication adjustment, wear inspection and other links to keep the equipment in the best working condition and extend its service life.
Emergency plans and disposal measures
For various emergencies that may be encountered during the installation process, such as equipment failure, unexpected downtime caused by operating errors, power system interruptions, severe weather changes, fire accidents, etc., detailed emergency plans and disposal measures should be formulated in advance. The emergency plan should include emergency command system, rescue team organization, information transmission process, on-site evacuation route and other contents to ensure that once an emergency occurs, the emergency response mechanism can be quickly activated to effectively control the development of the situation. At the same time, emergency response training should be provided to operating personnel. By combining theoretical teaching with field exercises, the rapid response capability and independent problem-solving ability of all personnel in the face of emergencies can be improved, ensuring that various emergencies can be responded to quickly and effectively at critical moments, safeguarding the safety of personnel lives and the smooth implementation of engineering projects.